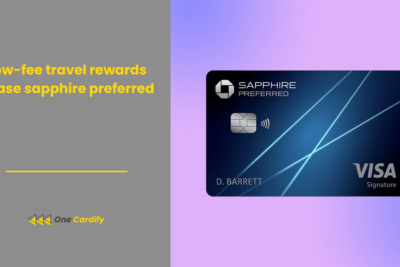
Predictive maintenance with IoT sensors
In the world of industry today, predictive maintenance on IoT sensors not only signals a new epoch of effectiveness and reliability for business but also represents a footprint of a major breakthrough machine production. This extended materials should not only will cover the topic through end-to-end but also demonstrate how modern sensors could start the revolution in the maintenance protocols, productivity, and cost reduction.With the integration of the IoT sensors, resulting in the predictive failure before it happens, company will then replace the part that causes the failure and reduce offline time. The transformation from a reactive to a preventive maintenance attention, in addition to the extension of machinery life cycle, also ensure a safe working place.This article gives you the roadmap from the basic understanding to the fully operational system of employing IoT technology for predictive maintenance. It acts as your guide and helps your business survive in the competitive market.
Introduction to Predictive Maintenance with IoT Sensors
IoT sensors powered predictive maintenance strategy is standing out as unique in a way that it have become the cornerstone of the smooth machine maintenance. Having the capability to recollect and assess the state of the machine throughout its run, these sensors are rightly instrumental to the process of early detection and prediction of the emerging problems.The maintenance schedules of traditional models evolve around the time or usage factors; this approach considers the insights from the sensors in real-time to determine the correct maintenance time. Here, unarranged appearances are significantly reduced, and maintenance is optimally arranged.The fact that the deployment of IoT sensors not only speeds up the operations but also leads to massive cost savings is plain. This means that cheats are no longer a problem as people can no longer replay a level and cheat or give themselves extra lives.Knowing the basic of the technology, such as types of the sensors and application of the data analytics, will prove quite useful for an organization to carry out a successful prevention routine. The guaranteed information ensures that the properly collected data is appropriately processed for meaningful insights into the data.
Related content
The Role of IoT Sensors in Predictive Maintenance
It is sensors IoT that keeps a watchful eye and makes possible the predictive maintenance strategies. They take the samples using thermometers, vibration sensors and pressure gauge which are the vital features of a equipment for their condition.The data handled by these sensors are prossesed by advanced analytics to find the odd cases or the deviations from the general standard. Thus it serves as a forewarning system for the equipment’s failure, so one can undertake preemptive action to deal with the issue.The adaptability of IoT sensors enables its usage in different fields. For instance, the manufacturing sector and the energy sector are just examples of the industries where this type of equipment is employed. In this sense, targeting available sensors and model analysis designs to suit specific business needs will automatically guarantee the best monitoring and maintenance outcomes.The introduction of IoT sensors involves a fine integration work which combines connectivity and data security aspects. Ensuring the predictability and safety of the sensors network is essential that the system should be successful.
Benefits of Predictive Maintenance
Predicting maintenance minimizes both the unplanned downtime and the cost of unnecessary repairs. This is go alway useful since it allows companies to remove causes of problems before they lead to production halts. This preventative maintenance can also be the case which in turn improves production effectiveness .Another characteristic would be the increased capabilities of the machinery in the way it would prolong its life span. The maintenance that is carried out regularly prevents rapid wearing out that leads to a breakdown. As a result, the equipment can operate much longer, thereby giving good returns on investment.Preventive maintenance along with this would lower risks caused by accidents. Through the avoidance of sudden equipment failures the chances of accidents hitting the workers hard are considerably diminished what is very beneficial in terms of the development of safe environment and maintaining reliability.The type of benefit noteworthy to include is decreasing energy use. That is that well-maintained machines are less likely to be the sole source of more energy consumption and are, in effect, a contributor of environmental sustainability.Finally, proactive approach is an aspect which ensures superior budgeting and financial planning. Businesses are able to put a hold on their money with a clarity of how the maintenance is run so that emergency and unscheduled repairs are less likely to happen.
Case Studies: Success Stories of Predictive Maintenance
A predictive maintenance by IoT sensors leveraged in several organizations across different sectors has led to many of the organization to noticeably and significantly improvements in their operations. Among their success stories, a manufacturing company reported that they have cut maintenance expenses by 30% while unplanned downtime went down by 25%.Switching to another example, we have the energy sector in which a grid utilizing IoT sensors was set to monitor the performance of generators. Unfortunately, in this kind of grid the performance was not as expected as the turbine availability and efficiency only increased by 20%.Such stories reflect the power of predictive maintenance in transforming the way businesses deal with daily challenges and, in so doing, continue to emerge as the major distinguishing factor in the current market.
Implementing Predictive Maintenance in Your Business
To successfully use the predictive maintenance, companies’s first thing must be its evaluation of the current challenges and strategies. This means establishing some indices like chosen equipment and desired parameters to be measured.It is for ensuring the appropriate technological infrastructure that will enable such crimes to be successfully punished. Sensing-as-a-service, constructing a stable model for data analysis, and integrating all these into the existing processes are the three main stages involved here.In addition to this training the human resource that will comprise the predictive maintenance system is equally important to be given a chance to understand and use it effectively. Educating employees about benefits and operational procedures enables seamless implementation of the system and thereby build more tangible impact.Besides this, it is simply necessary to control and improve the predictive maintenance approach repeatedly. The continuous process of inspection, assessment, and development enables adjustment to the needs of dynamic settings and upgrading of maintenance procedures.
Future Trends: The Evolution of Predictive Maintenance
The prospect of predictive maintenance looks promising, supposing the improvements of skills like machine learning or AI could make the process more accurate and precise. These technologies will provide even more capabilities for getting detailed executions of sensor signals, resulting in improved maintenance decisions.Another trend goes about predictive maintenance beginning to participate in the other industrial 4.0 technologies progress. By way of incorporating IoT sensors and digital twins, monitoring could be dialed up a notch to identify equipment performance and maintenance requirements.As the technology will evolve, we will notice that wider use of predictive maintenance is coming and this will shift it for many industries regular work practice, what makes predictive maintenance the standard for operational excellent.
Conclusion: Embracing the Future of Maintenance
The predictive repair along with IoT sensors represents a pivot towards the more productive, dependable, and low costing operations. Through the utilizing of the data and foresight gathered from the sensors, businesses can get head of the situation that may happen ahead of time, hence ensuring that the systems and machines as well remain in good condition.The road to predictive maintenance may be full of initial spending targeting on technology and trained personnel, but the advantages drawn from the lateral thinking are humungous in the form of reduced downtimes, extended equipment life span and enhanced safety.Forward, we see that the utilization of digital sensors in the industrial sector maintenance makes the future generations to redefine the current establishment as it sets the standards in the digital world.But actually taking advantage of predictive maintenance is not only about the acceptance of new technologies; it is also about keeping track of the future of the maintenance process that would work well in different areas of industrial activities.
IoT sensors are devices that collect and transmit data about their environment, such as temperature, pressure, or vibration, to help monitor and manage different processes or systems remotely.
Predictive maintenance uses real-time data from IoT sensors to predict when equipment will require maintenance before failures occur, unlike traditional maintenance that follows a fixed schedule or reacts to breakdowns.
Virtually all industries that rely on machinery and equipment, including manufacturing, energy, transportation, and healthcare, can benefit from implementing predictive maintenance strategies.
The main benefits include reduced downtime, extended equipment lifespan, increased safety, lower energy consumption, and better financial planning.
Challenges can include the initial cost of technology, the complexity of integrating new systems, ensuring data security, and the need for employee training.
Advancements in AI and machine learning are expected to enhance the accuracy of predictions and enable more sophisticated analysis, making maintenance decisions more efficient and reliable.
Yes, predictive maintenance can be integrated with other Industry 4.0 technologies such as digital twins, blockchain, and augmented reality to provide more detailed insights and improve operational efficiency.
Related Posts